PCBs play a central role in several key systems of rail trains, which are elaborated in the following three aspects: Automatic Train Protection (ATP) system, Automatic Train Pilot (ATP) system, and Train Communication Network (TCN):
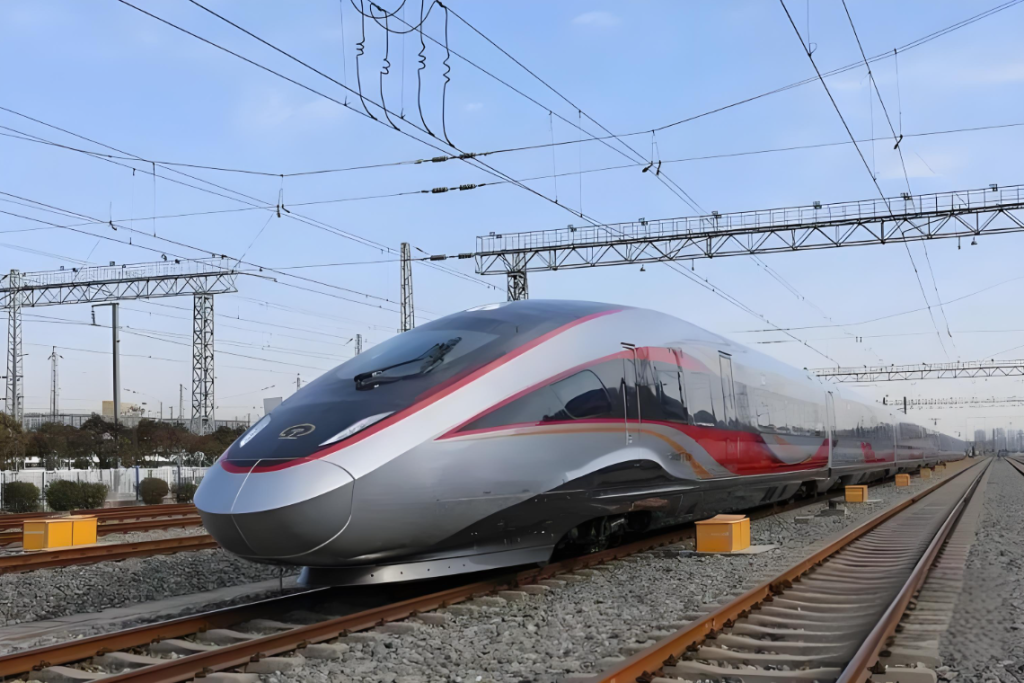
Automatic Train Protection (ATP)
Sensor Signal Processing
The PCB integrates high-precision sensor interface circuits and connects sensors such as speed, axle temperature, and track circuit. The collected data on train operation status is converted into electrical signals, which the microprocessor uses to quickly and precisely analyze and judge whether the train is running safely.
Brake Control Execution
Equipped with a powerful brake control circuit, when a safety risk is detected. When a safety risk is detected, such as speeding or approaching a danger zone, the microprocessor sends a braking command, which precisely controls the train’s braking system via the PCB. It realizes fast and smooth braking to ensure safe stopping.
Reliability Assurance Design
Redundancy technology and fault diagnostic circuitry are adopted. The redundancy design ensures that the system still has basic safety functions when part of the circuitry fails. Fault diagnostic circuitry monitors the PCB components and circuit status in real-time, detecting faults and taking measures in time to minimize the impact on train operation.
Automatic Train Operation (ATO)
Positioning and Navigation and Computing
The PCB integrates advanced positioning and navigation chips and algorithms and receives information from satellite positioning, track sensors, and odometers. It precisely locates the train position and direction to provide accurate benchmarks for automatic driving. The microprocessor calculates the optimal speed and acceleration curves in conjunction with the route and operation plan.
System coordination and linkage
Responsible for communication and coordination with other systems in the train, and maintaining data interaction with ATP to ensure automatic driving under the premise of safety. It is connected to the communication network to receive scheduling instructions and update plans and is linked with the door and air conditioning systems. Automatically opens and closes doors and adjusts the interior environment when stopping at platforms to enhance the passenger experience.
Train Communication Network and PCB
Multiple communication integration
The train communication network adopts Ethernet, CAN bus, MVB bus, etc., and the PCB integrates corresponding communication chips and interface circuits. The PCB integrates the corresponding communication chips and interface circuits to connect each device of the train to the network and realize high-speed and stable data transmission. For example, the Ethernet controller encapsulates and decapsulates data, and the CAN controller realizes CAN protocol functions for data conversion and transmission.
Reliability enhancement measures
Electromagnetic shielding, signal filtering, redundant design, and other protective measures are adopted. Reduce the impact of external electromagnetic interference on communication signals, ensure accurate and complete data transmission, and ensure stable and reliable communication of the train systems.
PCB plays a significant role in each key system of railroad train, provides solid technical support for its safe and efficient operation, and will continue to play an important role in the development of technology.